Tecnoplating
Architects: Alondra Figueroa & Fernando Maytorena
Date: November 2013
Tutor: Antonio Riggen (Tec de Monterrey)
Location: El Salto, JAL, México
Software: Rhino, 3ds Max, VRay, Photoshop & Illustrator
Fabrication Technique: 3D Printing & Laser cutter
Physical Model Materials: 3D printed powder, MDF and bakery paper.

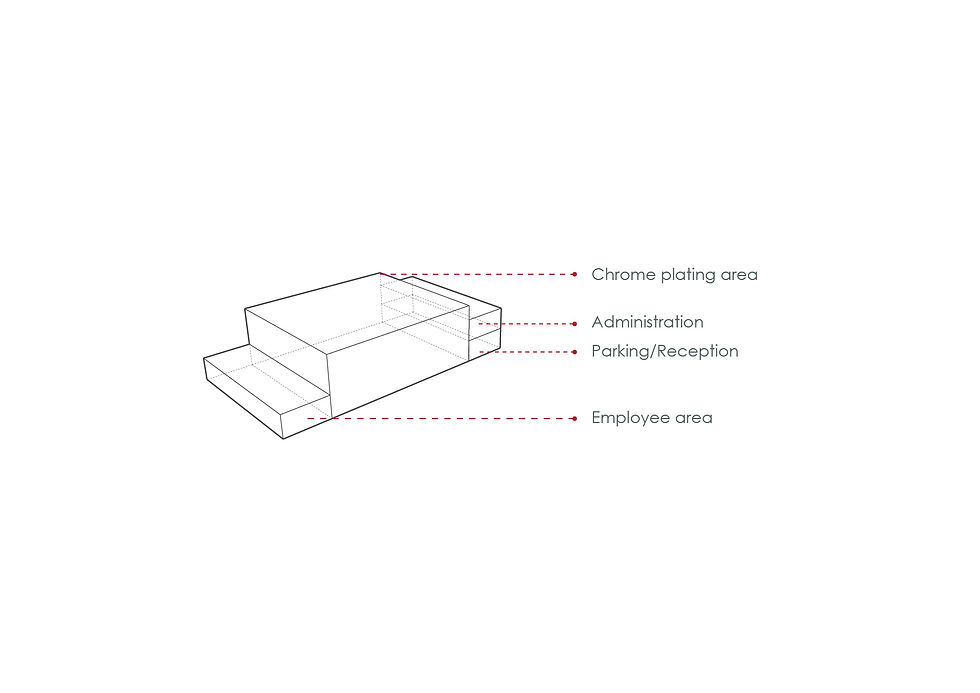


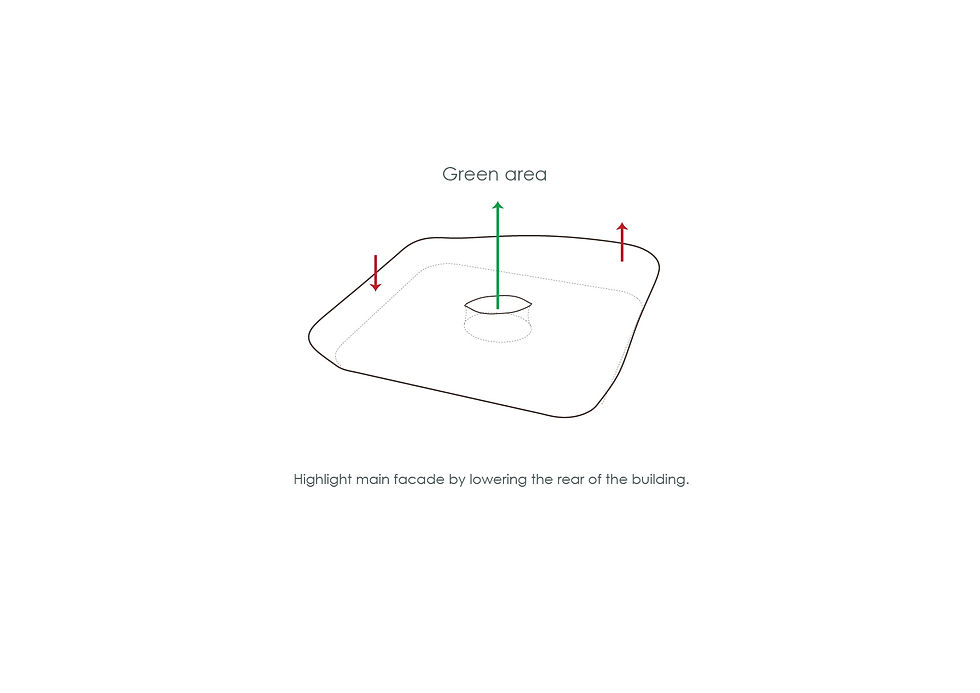

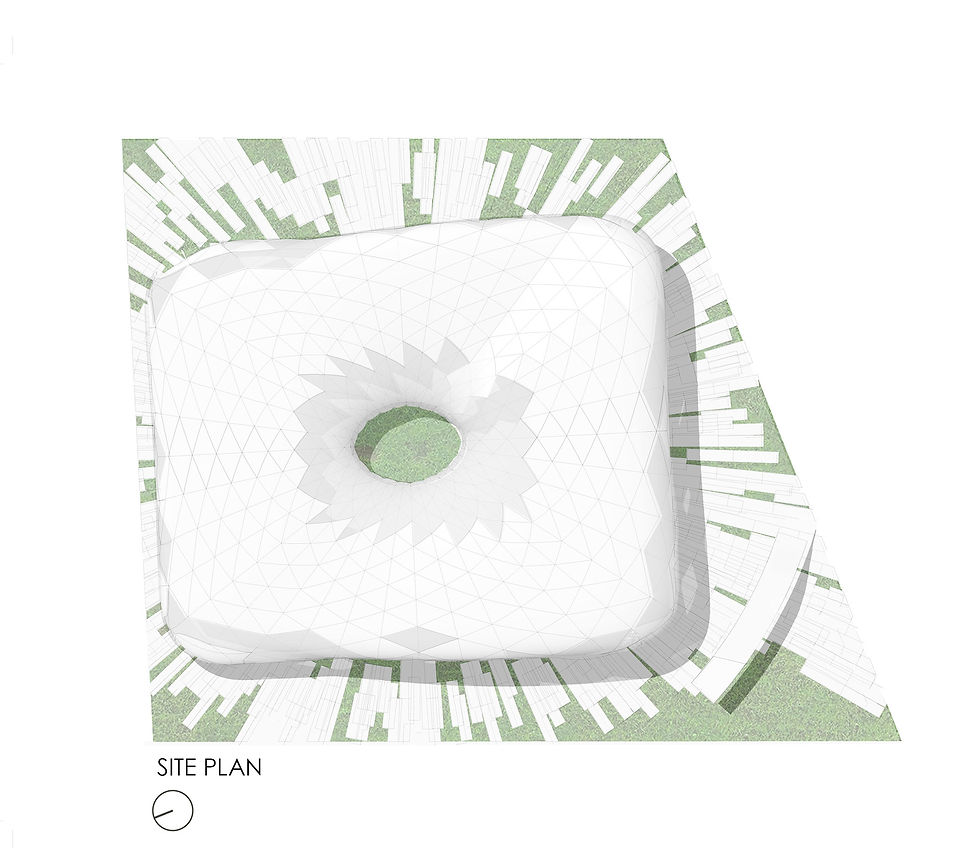




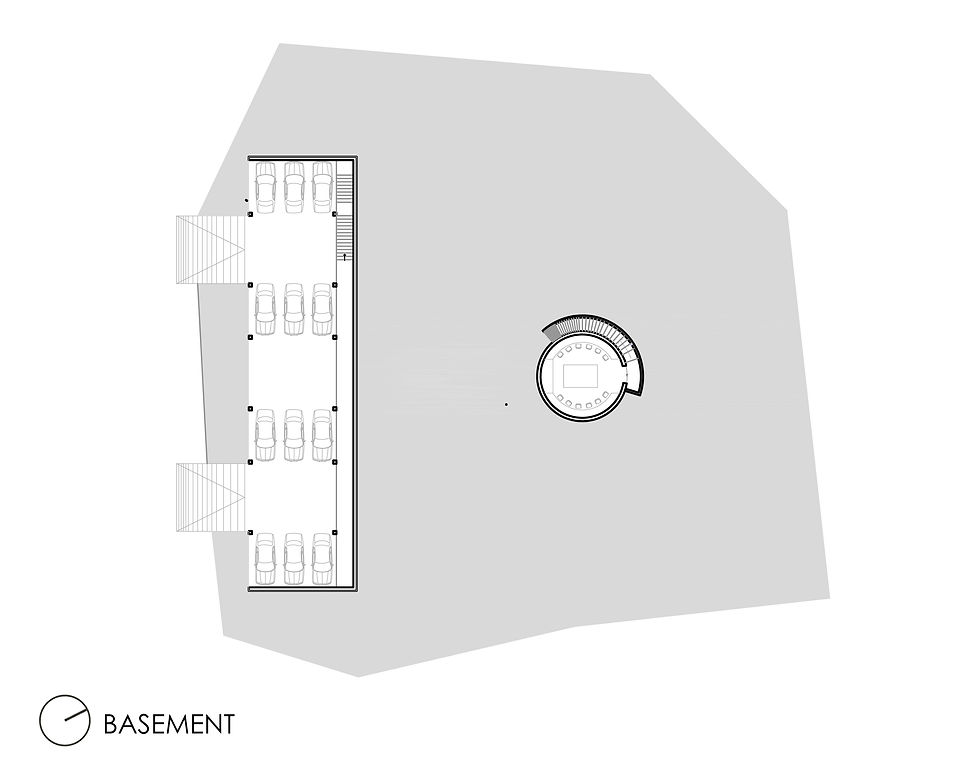

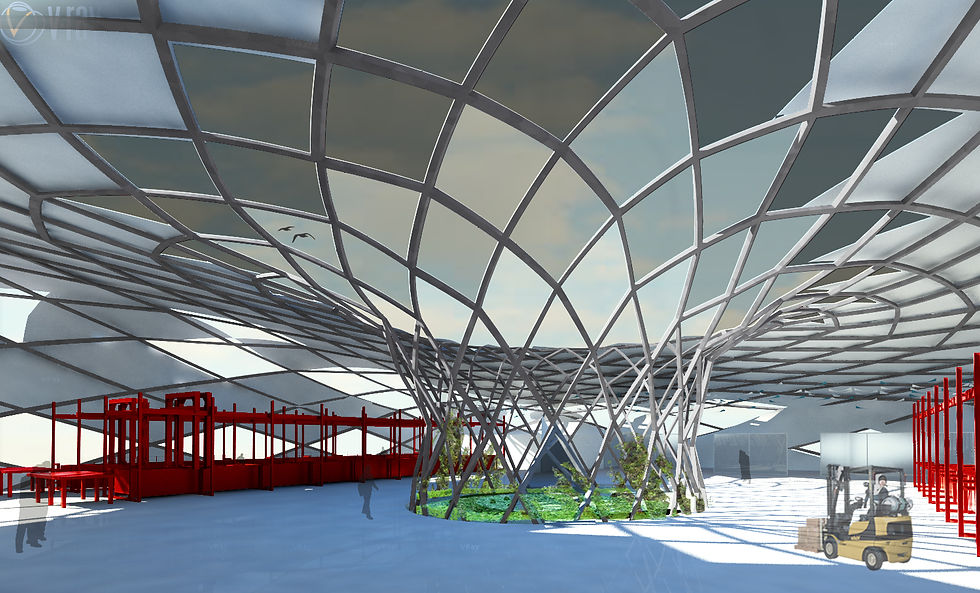


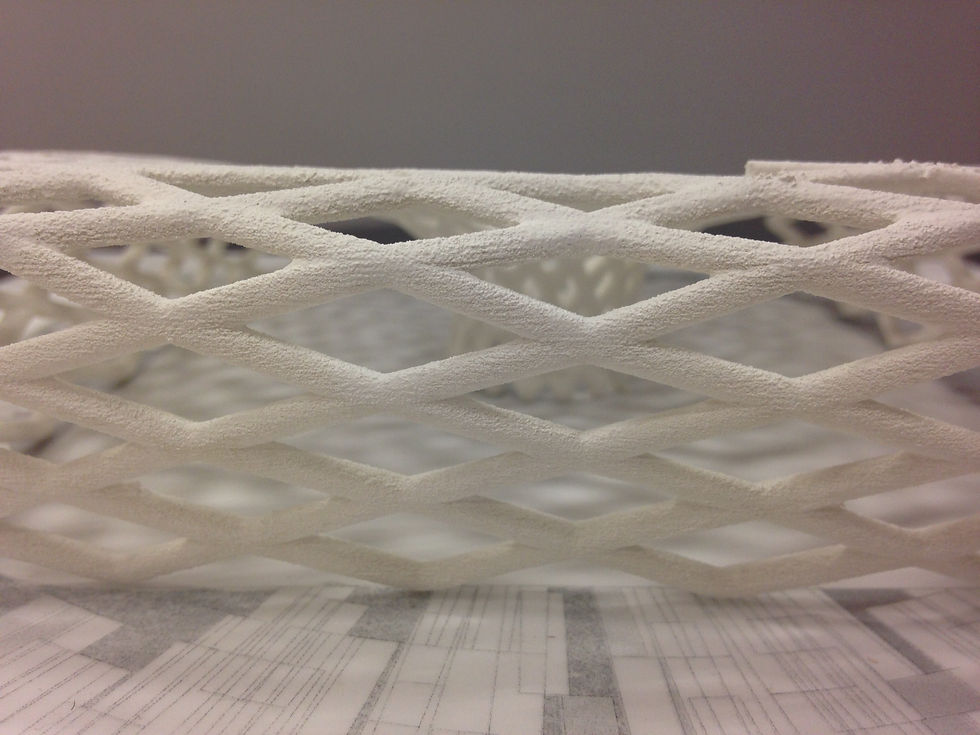

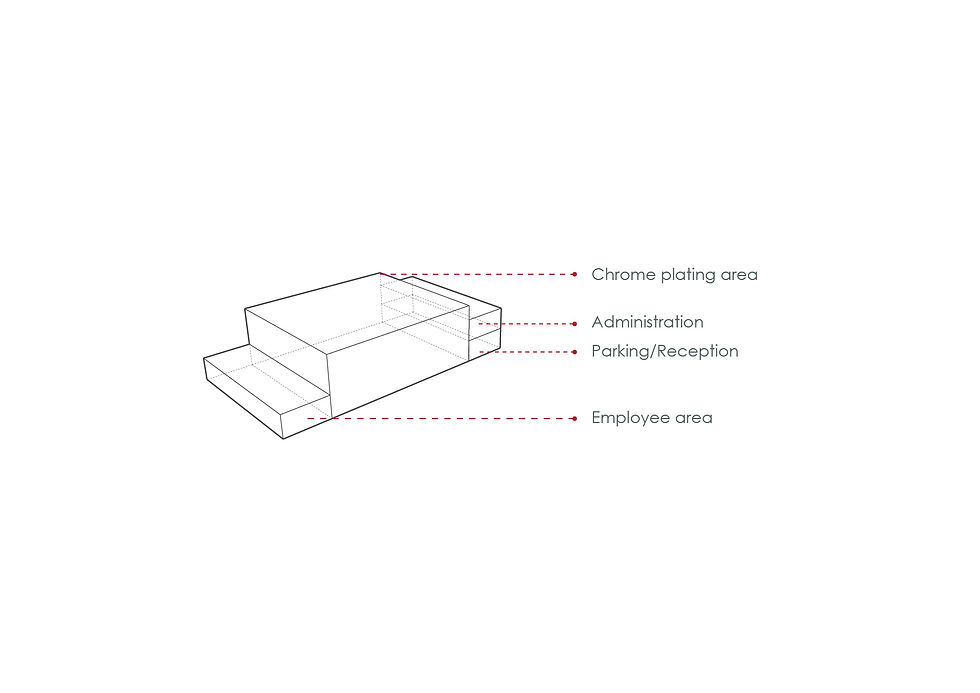


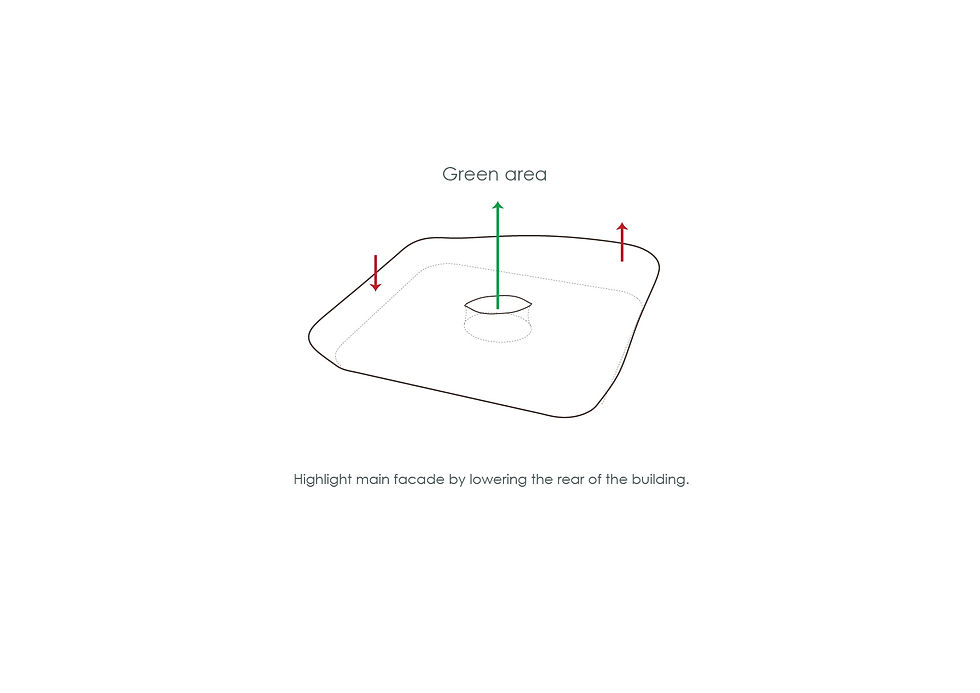

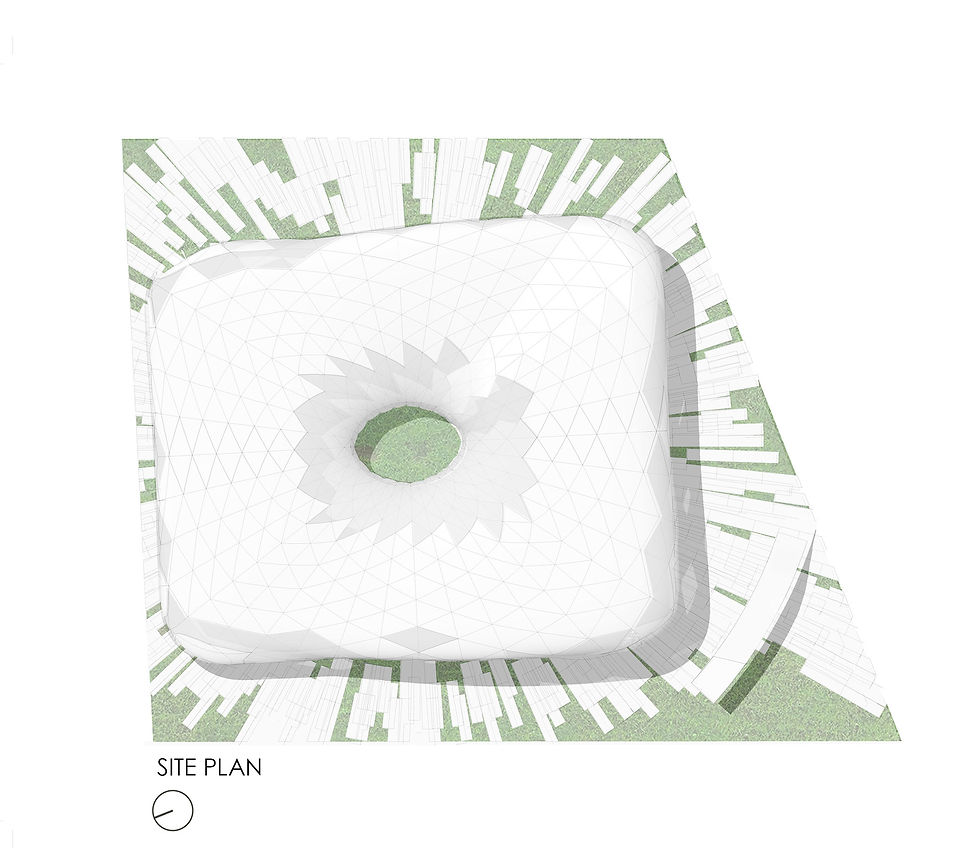




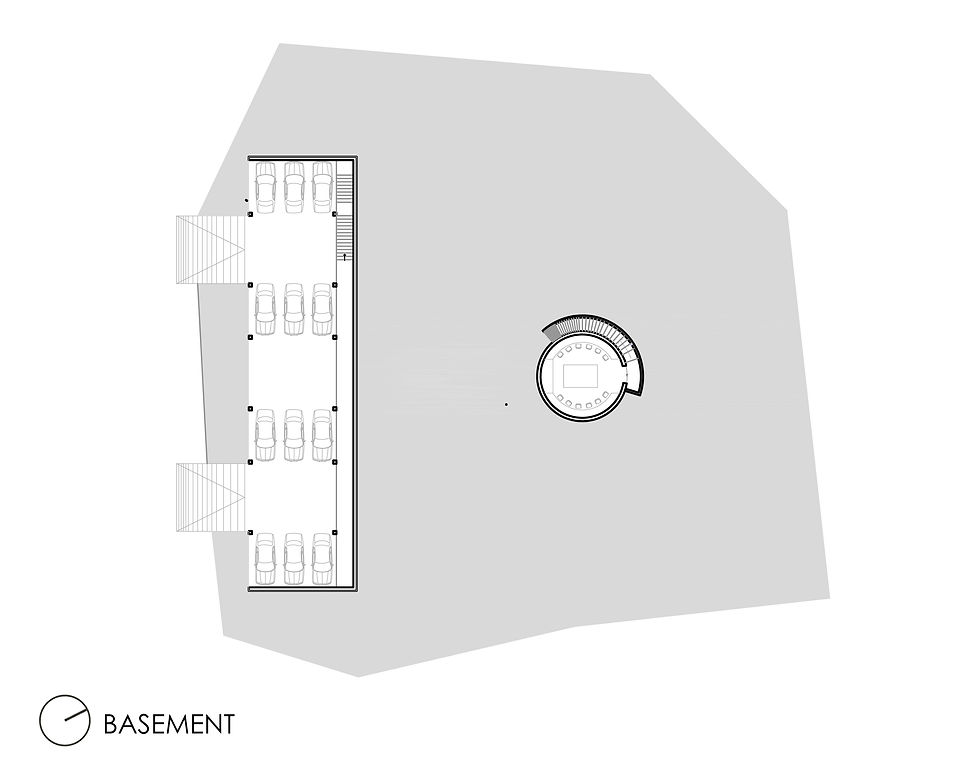

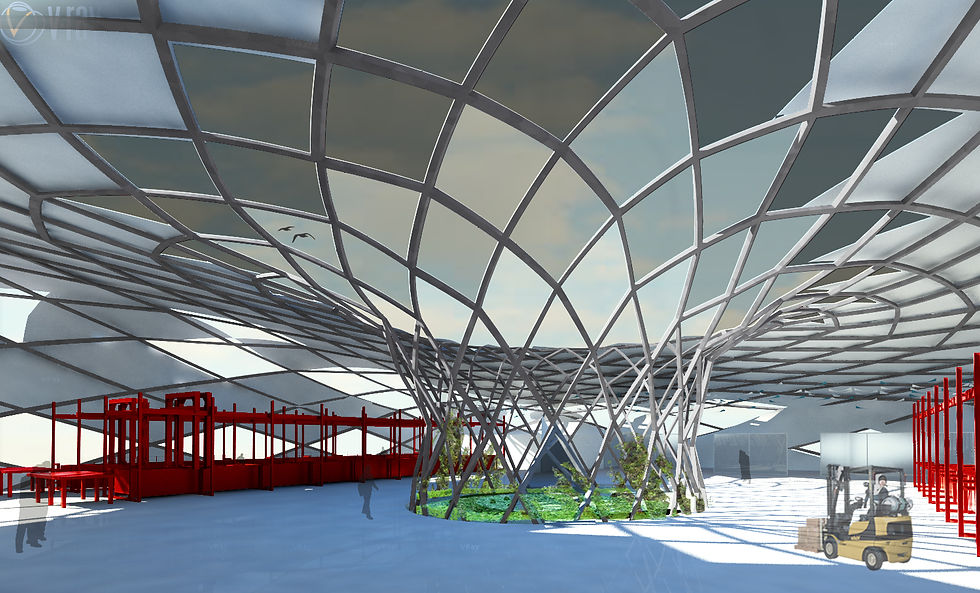


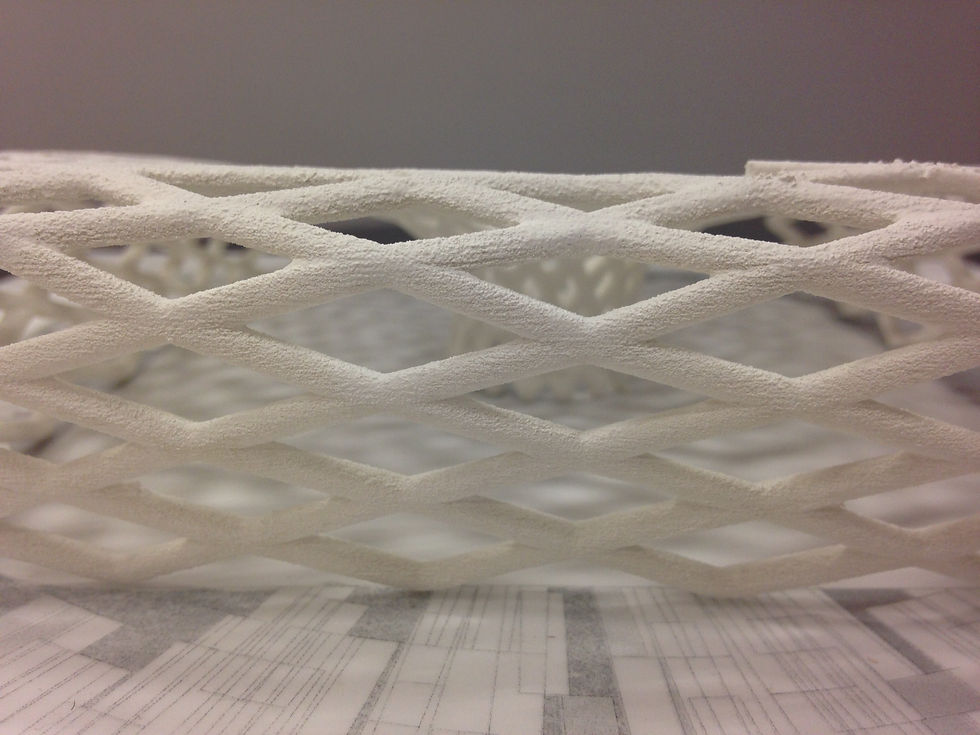
Tecnoplating project plans the construction of a factory in El Salto, México for a chrome-plating company using innovative computational and manufacturing techniques. The client had two special requests: first, that the aesthetic of the building wasn't that of a typical "boxy" factory, it should act as an architectural landmark for the surrounding area; and second, that bioclimatic design and passive solar systems be highly explored in order to reduce energy bills.
So, to achieve a more dynamic and smooth aesthetic, we proposed a double curvature aluminum-clad surface supported by a shell-like steel structure to envelop the building. The structural system favored an open plan and the large span required for the optimal functioning of the factory.
In order to harness bioclimatic benefits, glazed panels were placed in strategic spots to maximize both natural light and cross-ventilation for an ideal thermal comfort. A large green area sits in the middle of the factory, again to maximize natural light, but particularly to grant employees a breathing area, a space to escape from the tediousness that characterizes factories. Lastly, different sustainability features can be found on the project, including a greywater recycling system to water green areas and an automated artificial lighting system.
Tecnoplating 2.0
Architect: Fernando Maytorena
Date: December 2015
Tutors: Diego García (ControlMAD) & David Serrano (RandomARQ)
Location: El Salto, JAL, México
Software: Rhino, Grasshopper, Ladybug, Kangaroo & Karamba.
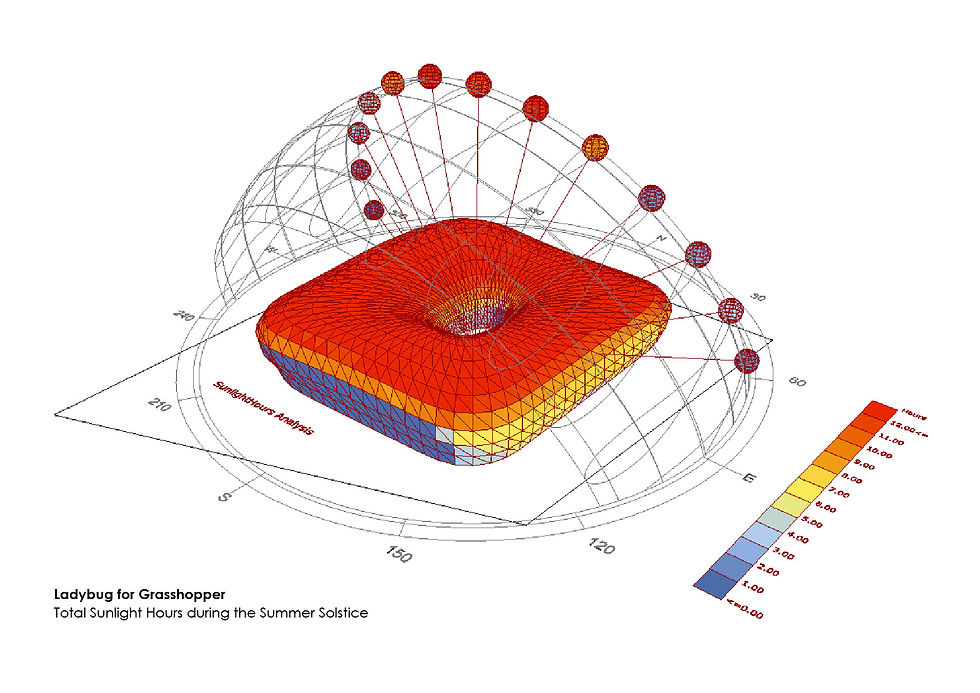




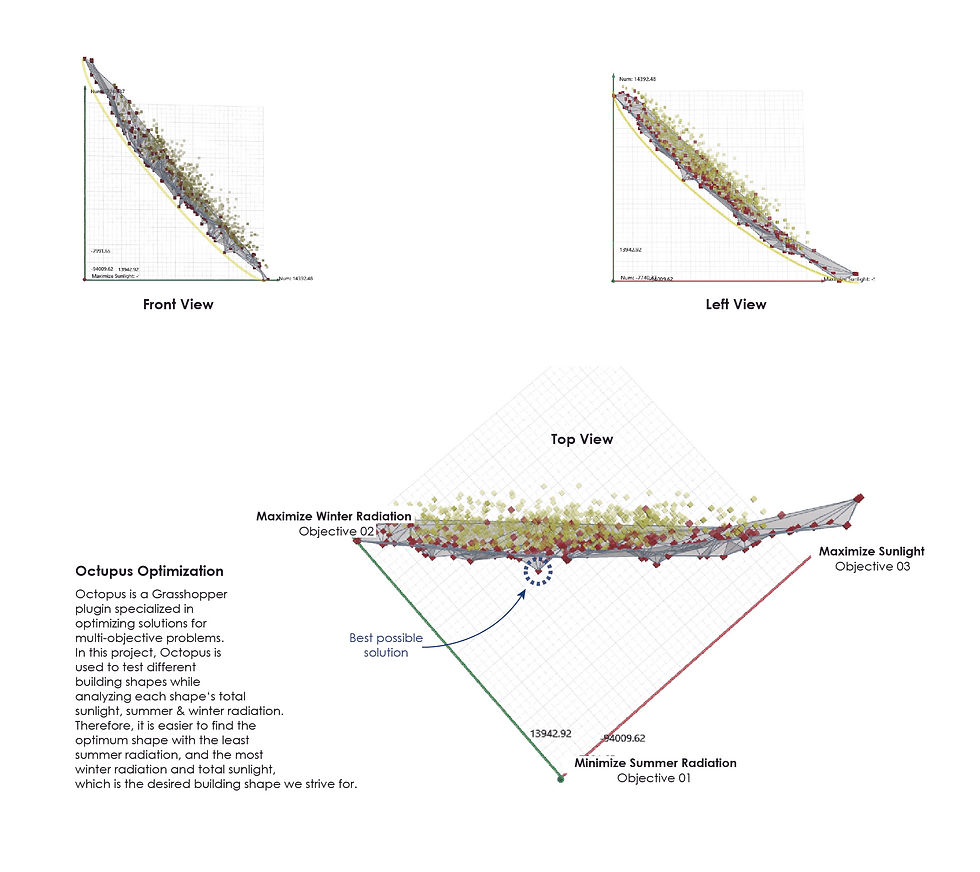





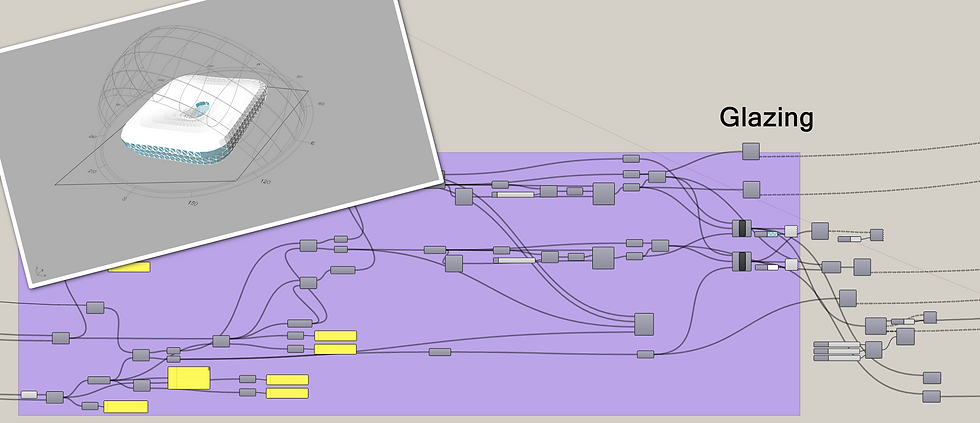





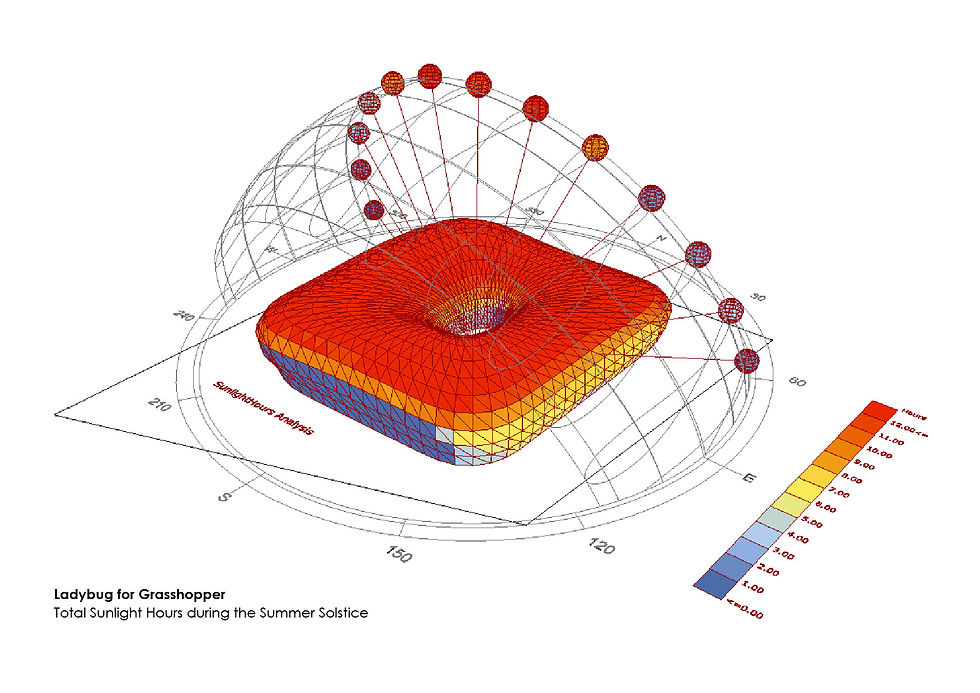




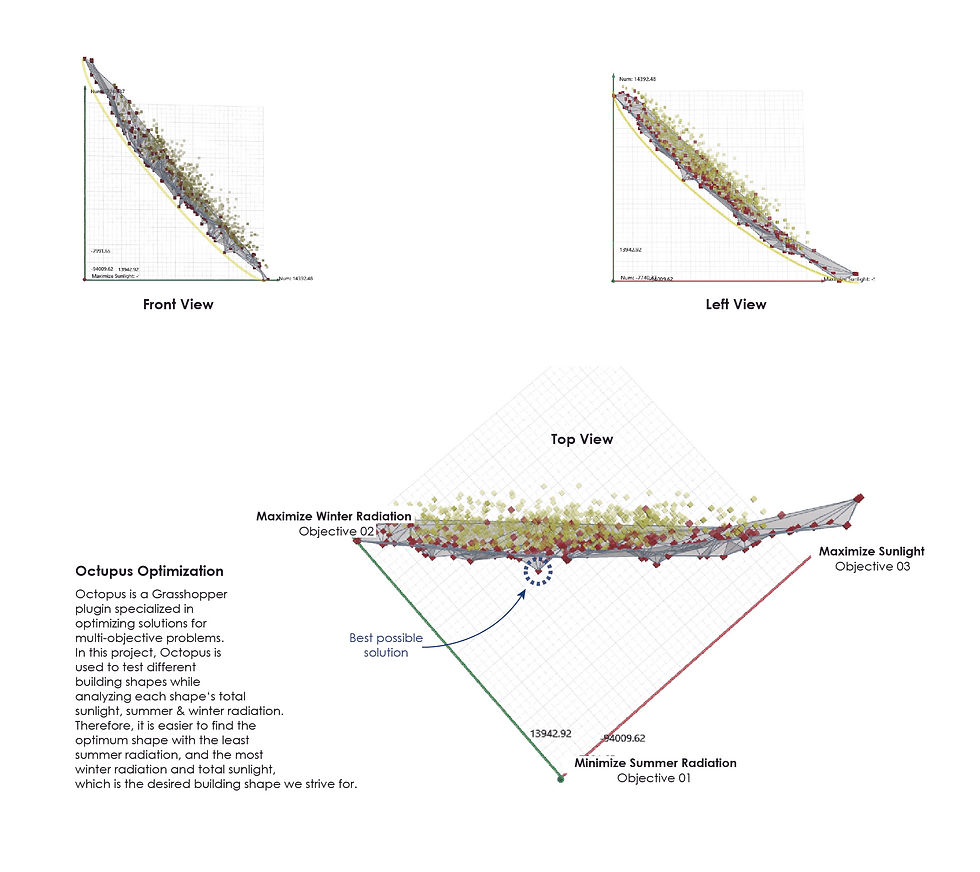





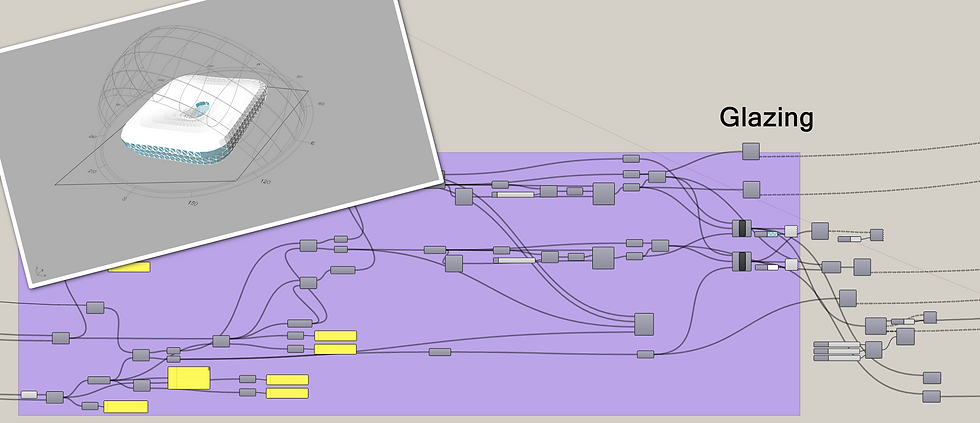





Tecnoplating project plans the construction of a factory in El Salto, México for a chrome-plating company using innovative computational and manufacturing techniques. To ensure that the client's requests be met and to facilitate the factory's construction process, different computational strategies were implemented.
For environmental simulations, Ladybug (an environmental plugin for Grasshopper) was used early on the design process to analyze solar radiation and sunlight hours during summer and winter solstices. Afterwards, Octopus (a multi-objective optimization plugin for Grasshopper) was used to better orient the building in relation to the Sun and to transform the initial geometry to reduce radiation during summer, increase radiation during winter, and maximize sunlight hours throughout the year; all this while maintaining a similarity with the starting form, thus minimizing deformation from the original massing. Also, radiation and sunlight hours results guided the decision on glazing ratio and location. Then, Karamba was used to analyze the deflection for the structure and to optimize the dimensions of the cross-section for each beam. Therefore, computational strategies helped maximize natural light & reduce direct heat gain.